ダイレクトギヤミーリング(DGM)の技術的詳細紹介
DGMの技術的な詳細を紹介しています。
マニアックな方だけ、ご覧ください。
※以下の画像はクリックすると拡大します。
DGMの概要
DGMの加工原理(歯形)
DGMの加工原理はを一言で述べると、インボリュート曲線の性質を利用しして、ホブカッター"が通る軌跡に沿ってDGMの工具(ミーリング工具)をトレースさせることです。
下の図のように、歯車はホブカッター(ラック)と基準ピッチ円と歯切ピッチ線で円と直線が滑らずに接触して転がる関係で噛み合います。下の図ではDGMの工具はディスク型カッターの例で描いていますが、DGM工具の圧力角とホブカッターの圧力角が一致していなくても、”圧力角修正角”を与えて工具の位置決めを加工設備で行うことで、ホブカッターの通る軌跡をDGMの工具で忠実にトレースさせることが出来ます。
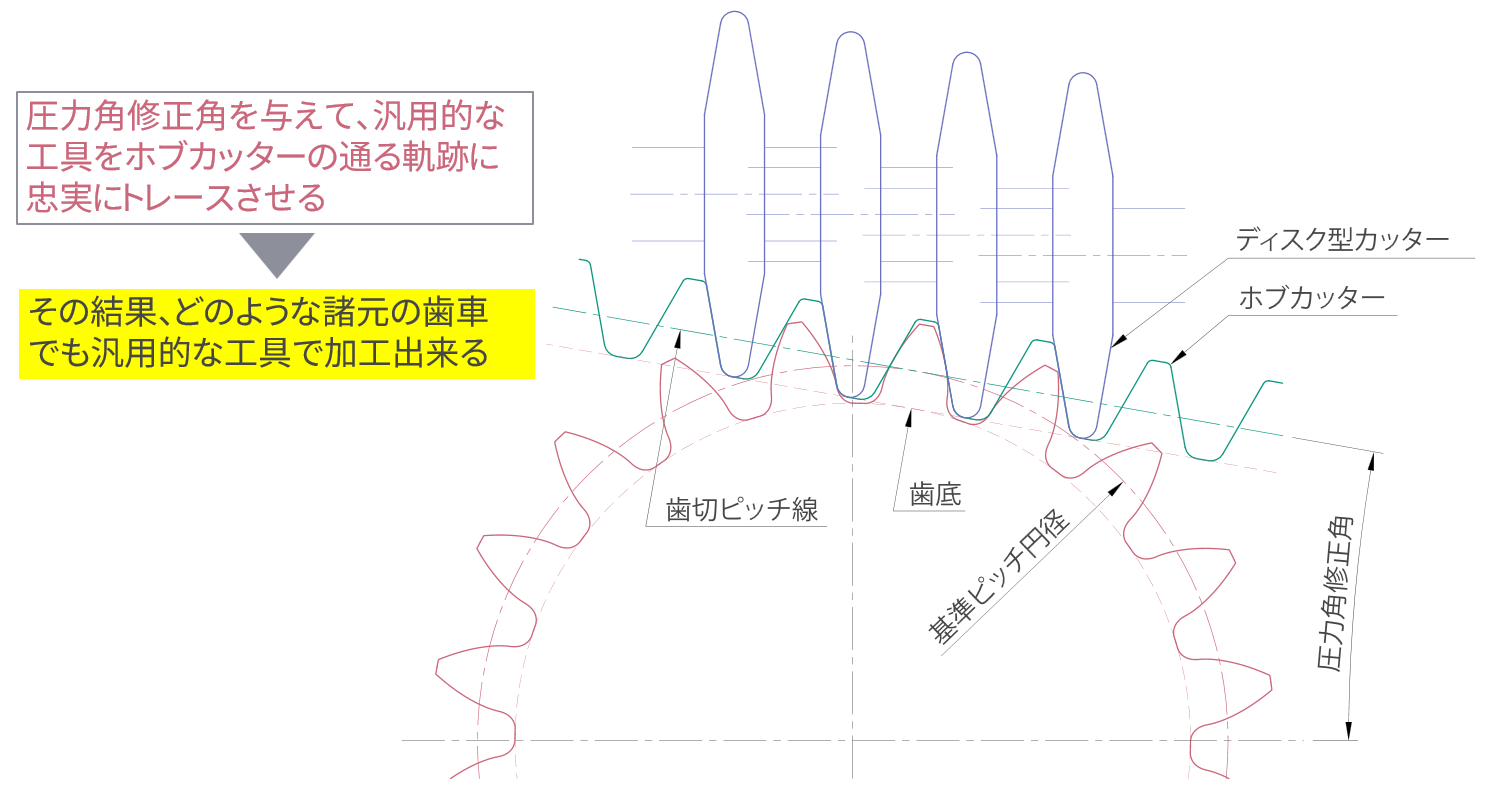
この原理を実際のNC加工機上に当てはめたものが下の図になります。
DGMでは、下図の ”NC加工機上の加工位置” と "DGM工具創成図" を自動的に描き、パスのチェックを行うことで、NCプログラムを作成していきます。
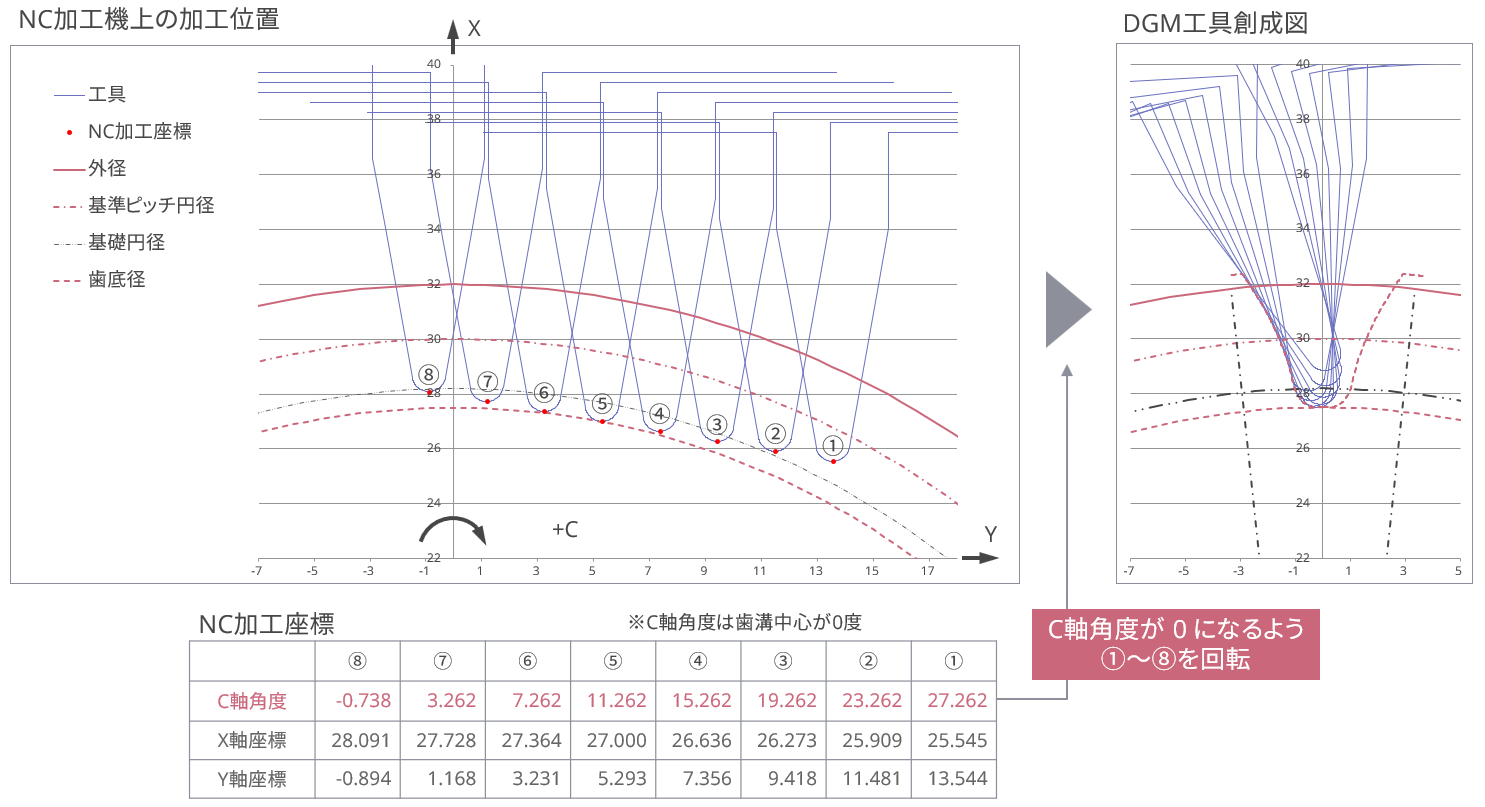
インボリュート歯面の曲線部はホブと同様にDGM工具の直線部で加工することになります。
これが歯車の歯形方向の形状を得ることが出来ます。
DGMの加工原理(歯スジ)
歯車は歯スジ方向にはネジであり、旋盤のネジ加工と同じく、下の動画のようにワークの回転と同期してリードに相当する送り量を軸方向に真っ直ぐ与えて加工を行います。
そのため歯スジを加工しているプログラムは下のプログラムの座標の中の、”G02” から始まる1行のみで点群データは使用していません。
"G01" ではなく、"G02(G03)" を使用している理由は歯スジにクラウニング(丸み)を与えているからです。
【座標情報プログラム】の中に、歯形方向の形状を与える加工座標をマクロ変数に与えて、【歯スジ加工プログラム】で歯スジ方向に工具を動かして加工を行います。マクロ変数が多く含まれて複雑そうなプログラムに見えるのは、歯厚・歯形(圧力角)・歯スジ(ネジレ角)・クラウニングなどの寸法を自在に調整するためのマクロ変数が必要だからです。
使用工具
CAMによる加工は基本的にボールエンドミルを使用して加工しますが、DGMは歯面のインボリュート部を工具の直線部で加工するため、エンドミルの場合の歯面仕上工具は、基本的にテーパーボールエンドミルを使用します。(スプライン等の歯丈が低い諸元の場合は。ラジアスエンドミルでも加工できる場合が多いです。)
ディスクカッターの形状は歯切工具であるウォームカッターと基本的には同じ形状ですが、様々な圧力角や特殊な歯丈(2.25m以上)に柔軟に対応出来るようにするため、圧力角が15度程度、刃先がフルRのものが使いやすく、DGM専用の工具を製作して使用しています。刃先Rの違いで何種類かの工具を準備しておくと、どんな諸元の歯車でも加工できるようになります。
DGM開発の一番の目的は、量産前の特殊な諸元の歯車を専用のホブカッターなどの歯切工具を製作することなく短納期の試作加工を行えるようにすることです。
その場合は、ホブカッターや研削砥石など円筒(円径)の工具が使用されるため、ディスクカッターが使用できる形状で歯車形状を設計されているいることが殆どです。
下の3種類の工具の図から見ても、ディスクカッターが圧倒的に生産性・加工の安定性が良いことは一目瞭然だと思います。
外歯のハスバ・平歯車の特殊歯車の試加工は、ディスクカッターでのDGMのような加工が大本命であるはずです。
歯車を加工するメーカーにとって必須の技術となってもおかしくなく、そのような世界を創造することが歯車加工技術研究所の目的です。
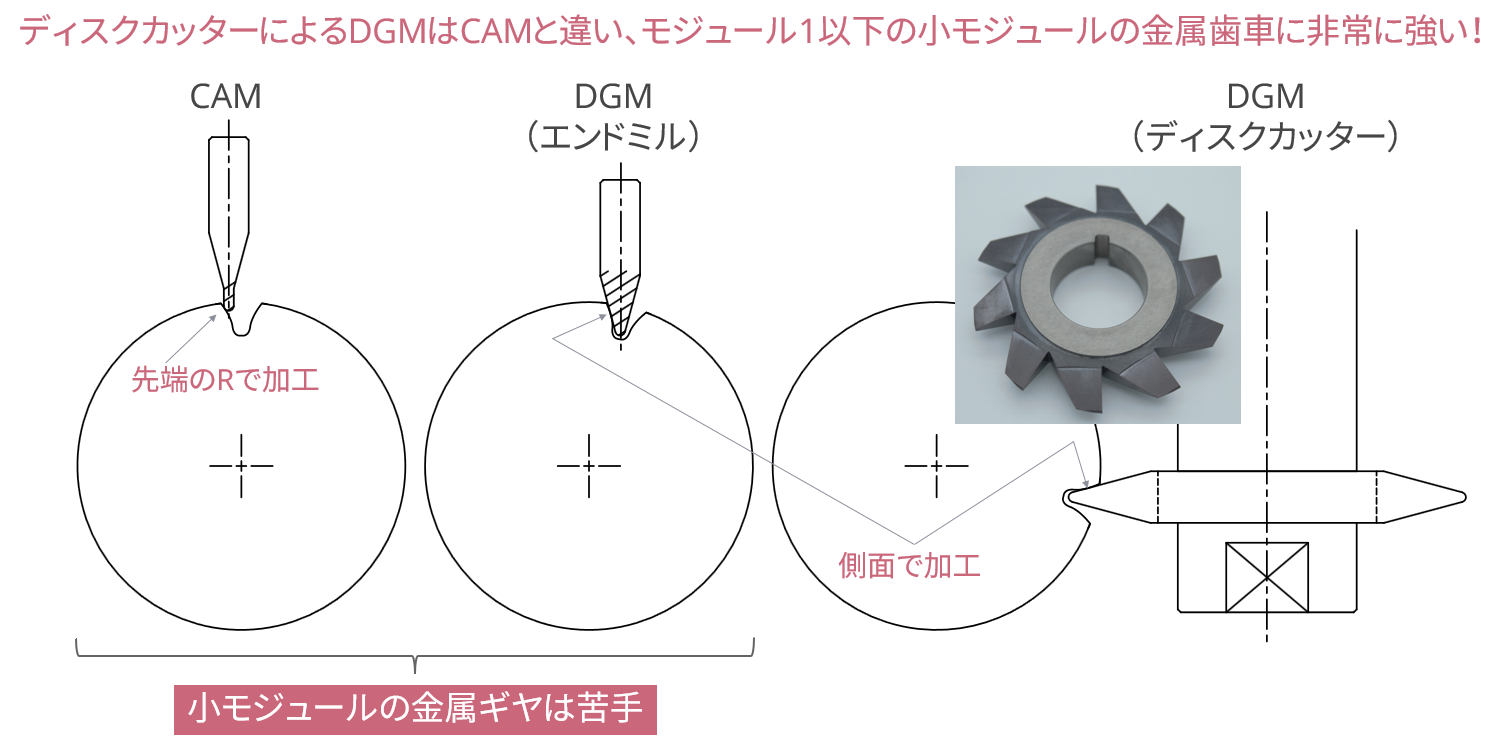
ディスクカッタは両側に圧力角のテーパーを設定しています。
両側のテーパー面をして加工することで、下の図のようにチャック側から工具を傾ける必要が無く、実際の加工現場で使いやすくなることを考慮しています。
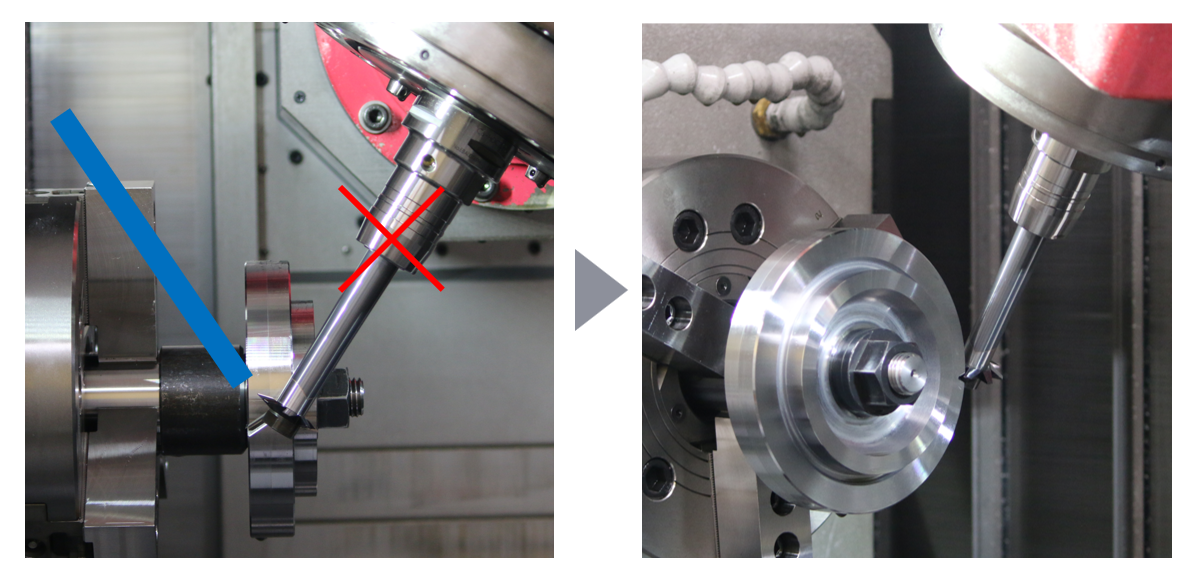
CAMとDGMの比較
下の表はCAMとDGMの比較を一覧表にしたものです。
加工時間は、モジュール 2 程度の歯車で、CAM(ボールエンドミル)で10時間かかる歯車の場合の、それぞれの加工方法のざっくりした加工時間のイメージです。
NCホブ盤でのディスクカッタを使用した加工が一番加工時間が短い理由は、工具を両側から支持出来ることから、切込量や送りを高くして加工できるからです。その分加工精度は粗くなります。
これら4つの加工方法が選択出来る場合は、断然ディスクカッターを用いた加工が有利となります。
その傾向はモジュールが小さいほど大きくなります。しかし、モジュールが1より小さいとホブ盤の両側支持の支持剛性の優位性は薄れてきて、汎用5軸NC加工機とNCホブ盤の差異は薄れてきます。
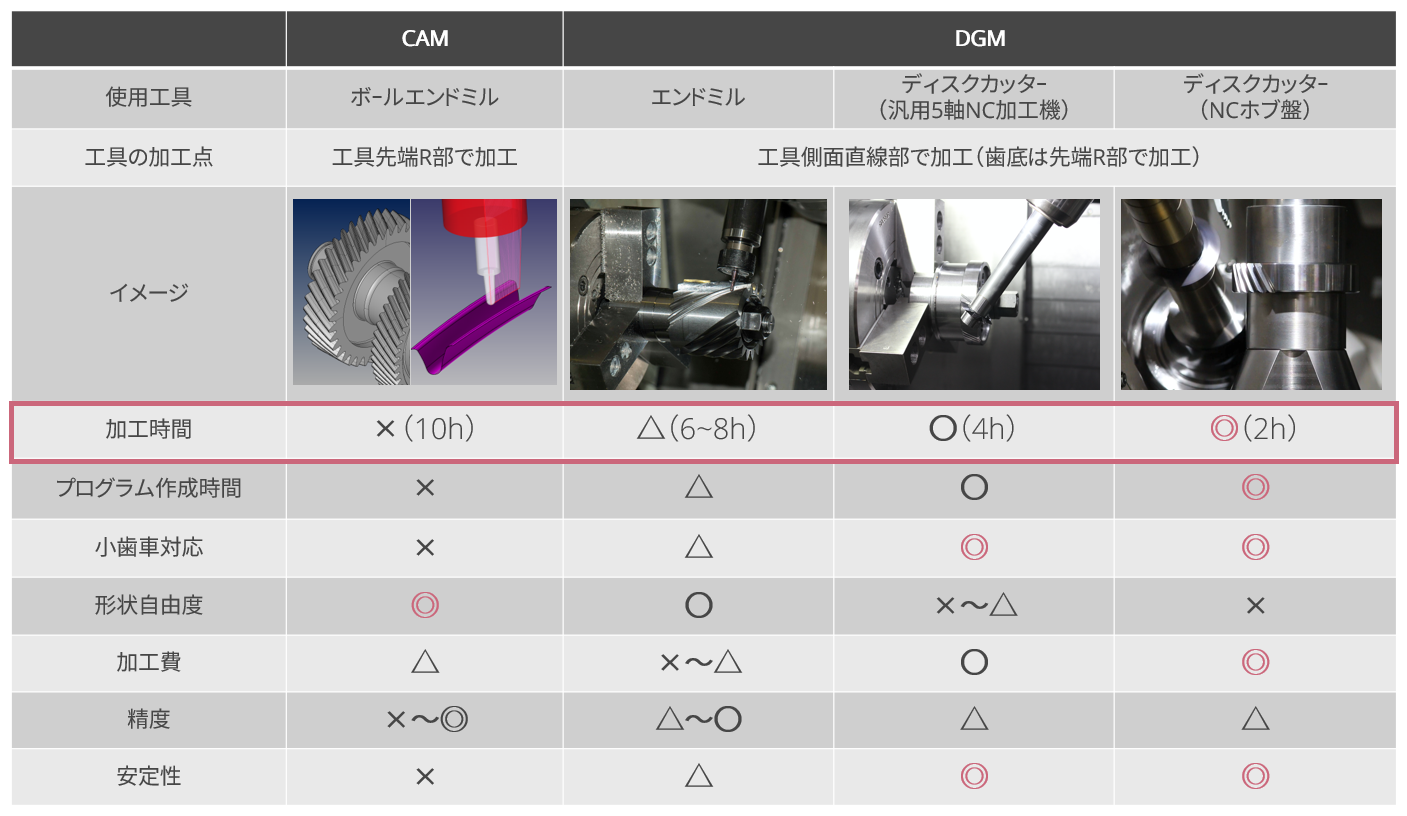
量産性が考慮されていないイレギュラーな形状がある歯車の場合は、CAMによる歯切りの出番となります。
通常の歯切方法に加えて、CAMやDGM等の加工方法の選択肢を持つことは、これからの試作歯切メーカーにとって、きっと、有利になってくるでしょう。
DGMの特徴
DGMは、ホブカッターの通る軌跡を忠実にトレースすることで、量産時のホブ切による歯底の隅R形状を忠実に再現出来ることです。
歯底部は歯の折損の基点となる部分のため、量産時の試作工法としては、歯底の隅R形状は非常に重要となります。
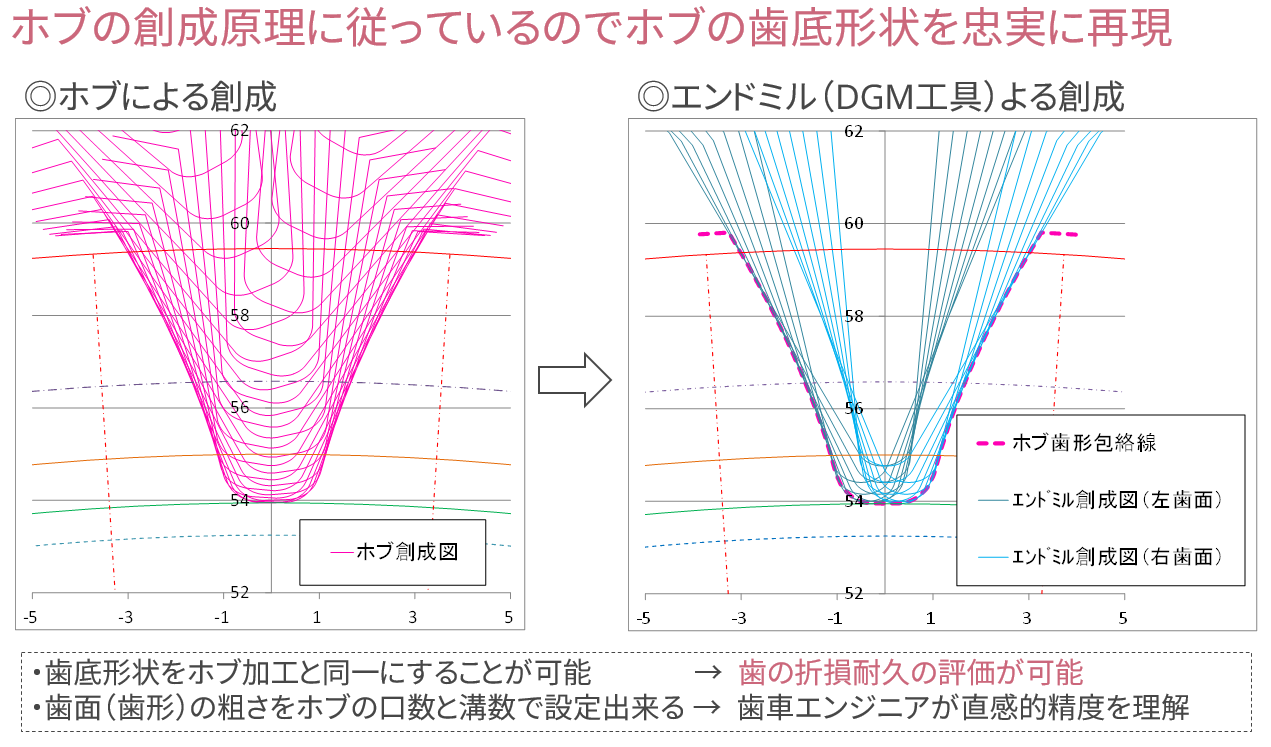
ソフトウェアは、歯車の加工者・生産技術者・設計者の視点を取り入れて、最近の5軸加工機のNC加工プログラムを作成しています。
歯車のインボリュート歯面は数学的には単純な数式で表せる面であり、CAM加工の面の法線ベクトルに合わせて工具を配置する考え方で、歯車歯面を加工することは出来ます。しかし、”温故知新” や ”不易流行" 等の言葉のように、今までのホブ加工や歯車研削加工の原理を知ったうえで、それを新しい5軸加工機に展開することにも大きな意味があると思います。DGMはそのような加工技術です。
NC5軸加工機のオペレーターがDGMによる歯切を習得すると、最初は歯車の専門用語等で苦労することもあるかもしれませんが、一流の歯車加工の知識を身に付けることができ、NCホブ盤等でも、すぐに仕事が出来る知識が身に付きます。
逆にNCホブ盤のオペレーターがDGMを習得すると、NCプログラムやNC加工機(旋盤やマシニングセンター等)に興味を持つ良いきっかけになるでしょう。
DGMによるNCプログラム作成手順
ホブによる創成図描画
DGMは加工対象部品のホブ創成図を描くところから始めます。
歯車の諸元を入力すると自動的にホブの寸法が計算され、そのホブを用いて加工する創成図が描かれます。
逆にホブの図面からホブの寸法を入力して創成図を描くことも出来ます。その結果加工される歯車の歯底径・面取り発生径・フィレット発生径等のすうちも計算されます。歯先面取り(セミトップ)・プロチュバランスにも対応しています。
歯厚変換や歯研等の取り代付与の計算がスムースに行えるよう、作り込んでいます。
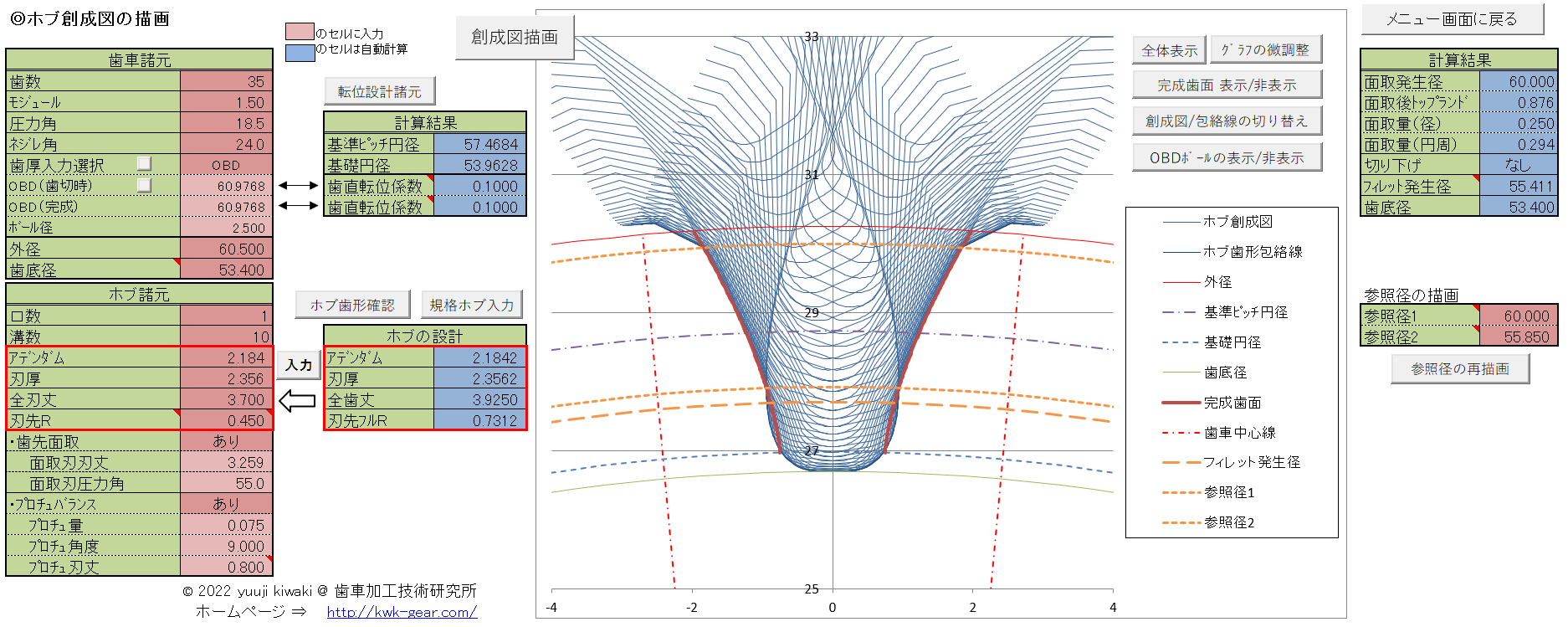
以下の画面では、歯先面取り(セミトップ)やプロチュバランスバランスを付与するために、それらのホブ寸法を計算し、ホブの形状を描画して確認することが出来ます。
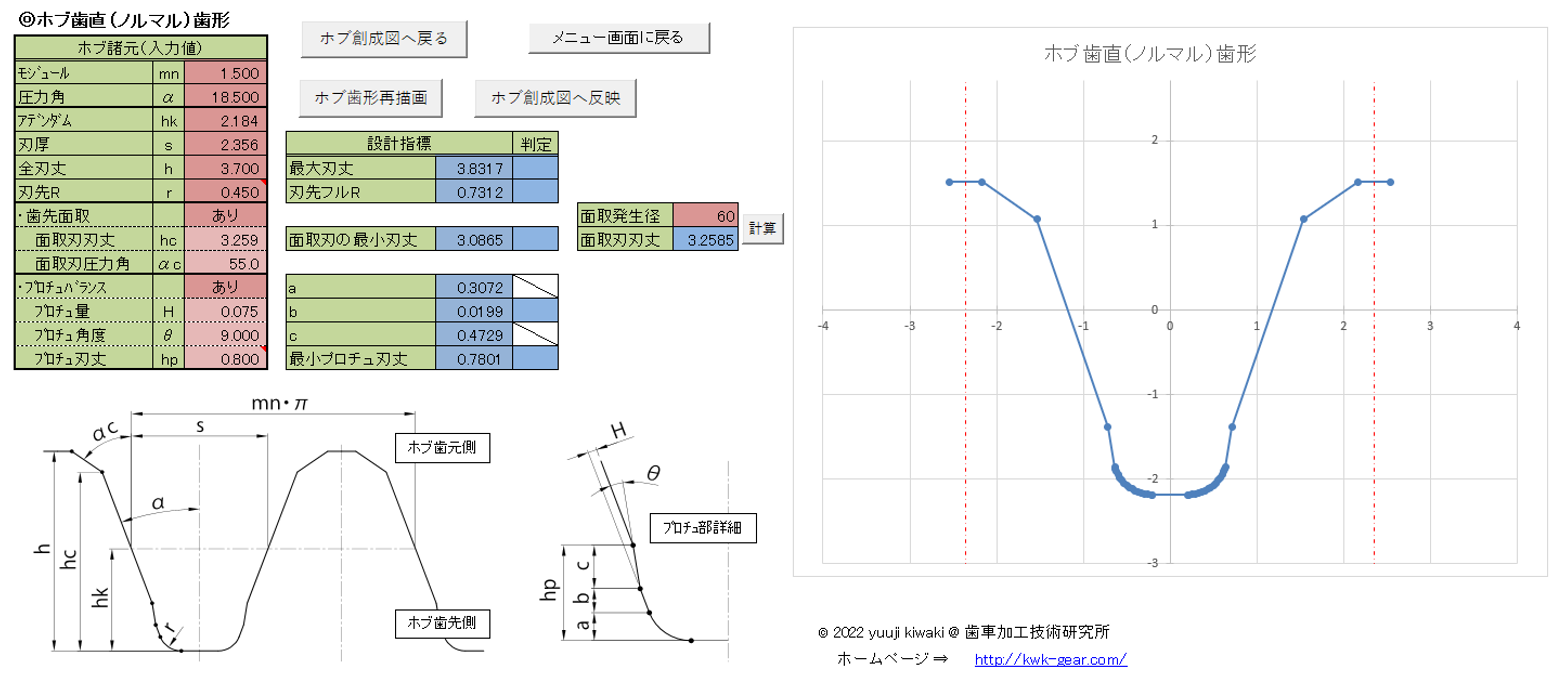
DGM工具による創成図
ホブによる創成図から得られた歯形包絡線に対して下図のように確認しながら、粗加工・歯面粗加工・歯面仕上加工などのDGMの加工パスを配置していきます。
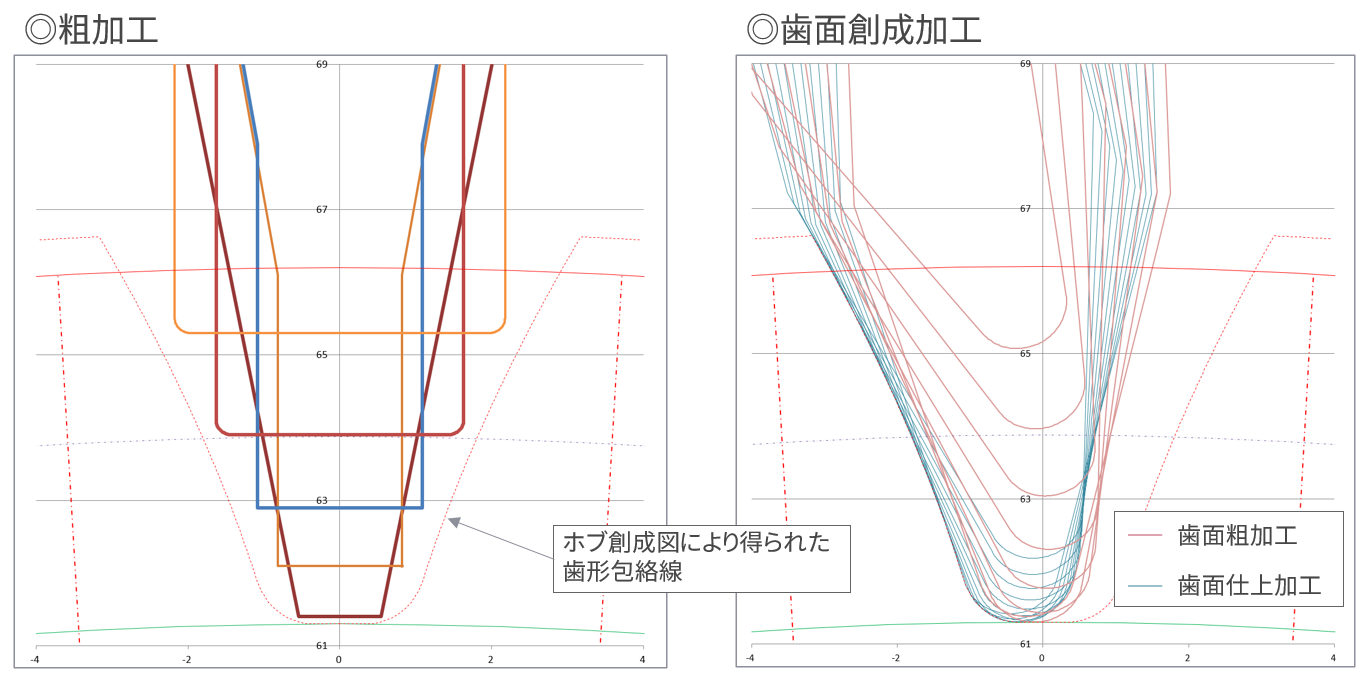
歯先面取りやプロチュバランスも下図のように加工パスを作成します。
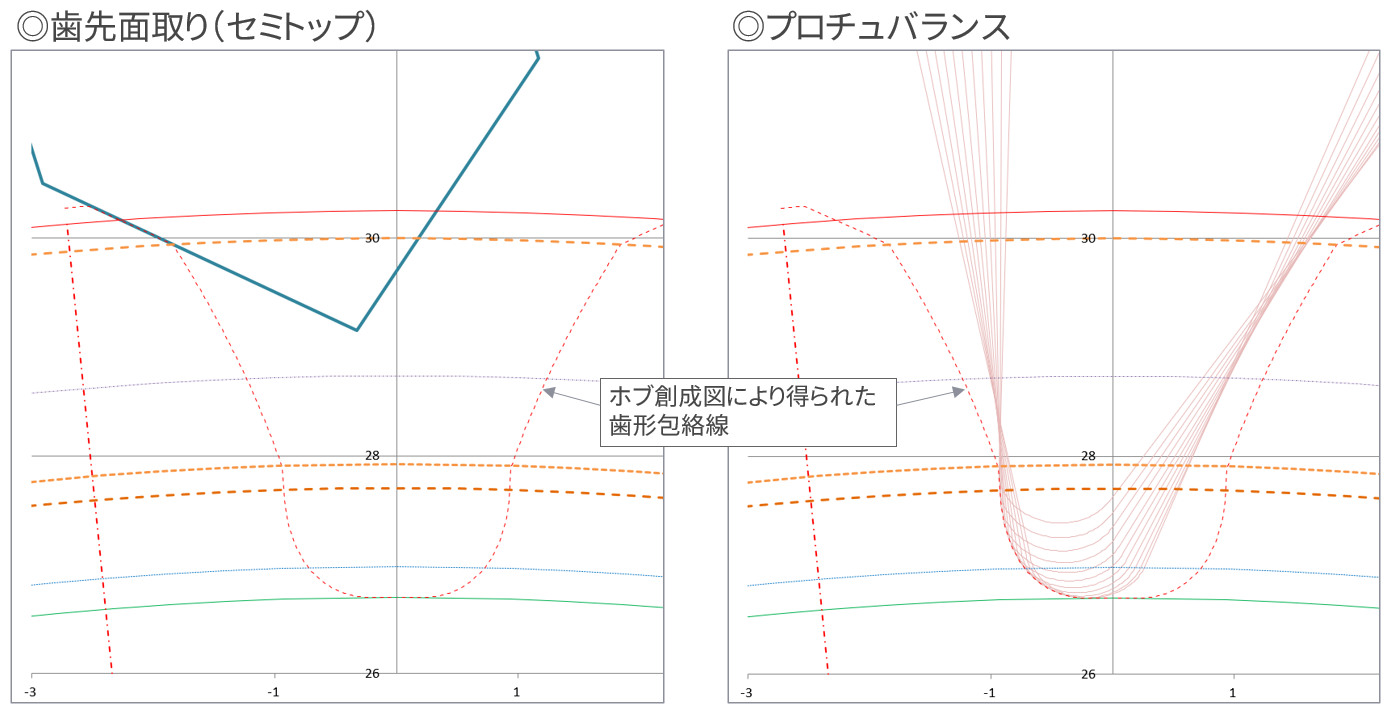
ホルダなどの干渉確認
歯形形状のパスを作成した後、エンドミルでは歯車外径とホルダの干渉、ディスクカッターでは歯車外径とシャンクの干渉を下図のようにチェックします。
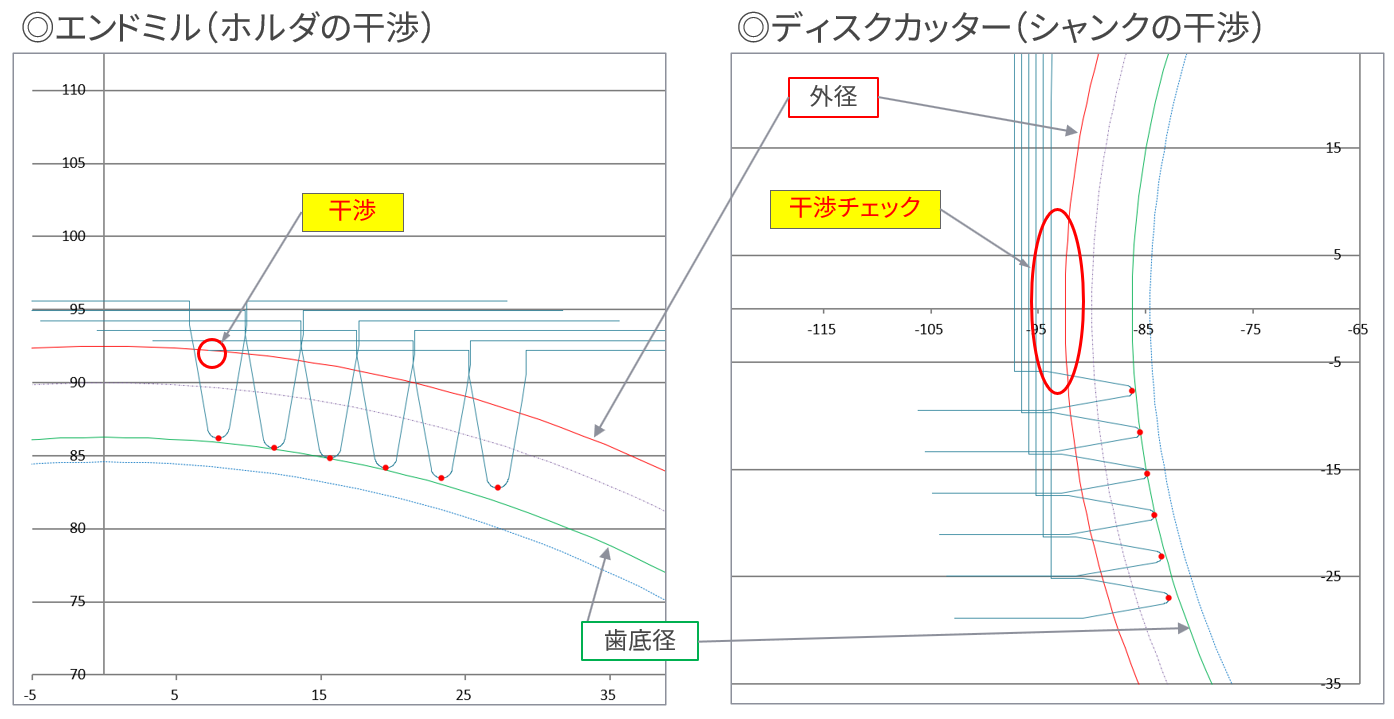
寸法調整可能項目
下表の項目を調整可能です。
切れ上がり形状やダブルヘリカル等の対応は、少し難易度が上がりますが、先述の歯スジ加工プログラムを修正することで対応可能になります。
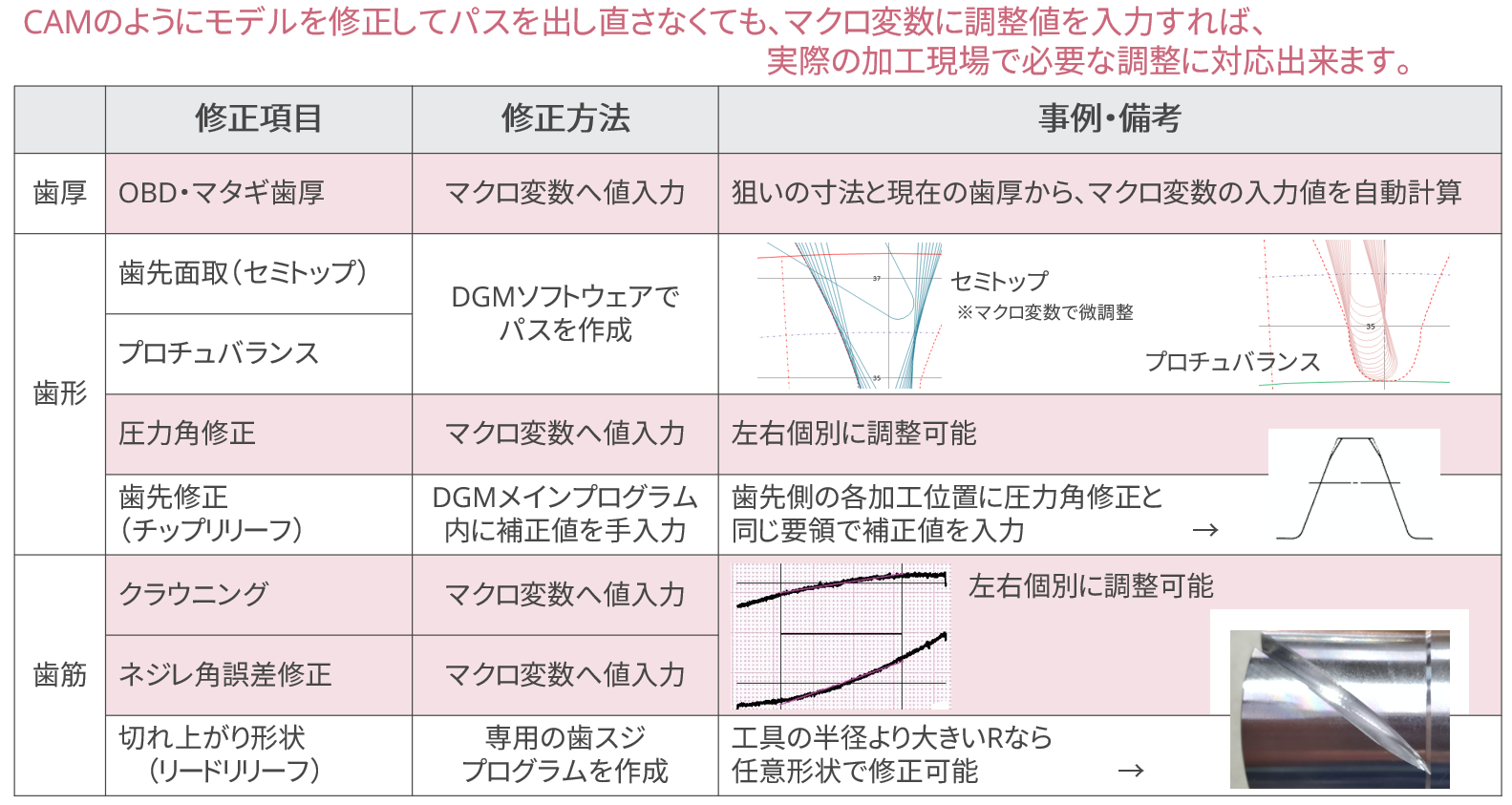
1歯加工して歯厚寸法や歯車精度を測定した後、下の画面で修正量を入力すると、修正に必要なマクロ変数の値が計算されます。この値を設備に入力すれば、CAMのように計算をし直して再出力する必要はありません。
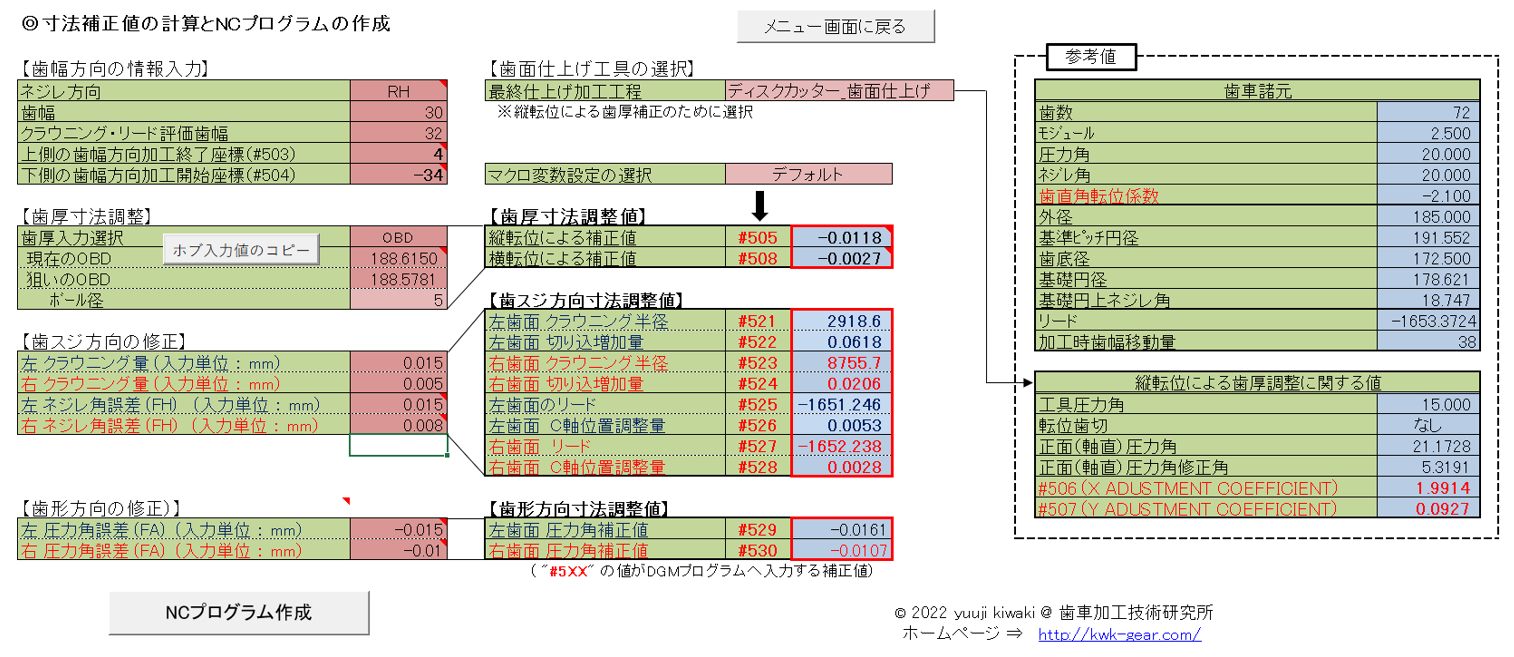
下の図は圧力角やネジレ角誤差を同じ歯車で調整した事例です。
歯車精度の等級を気にされるお客様が多いので、コメントを書いたのを、そのまま画像にしています。
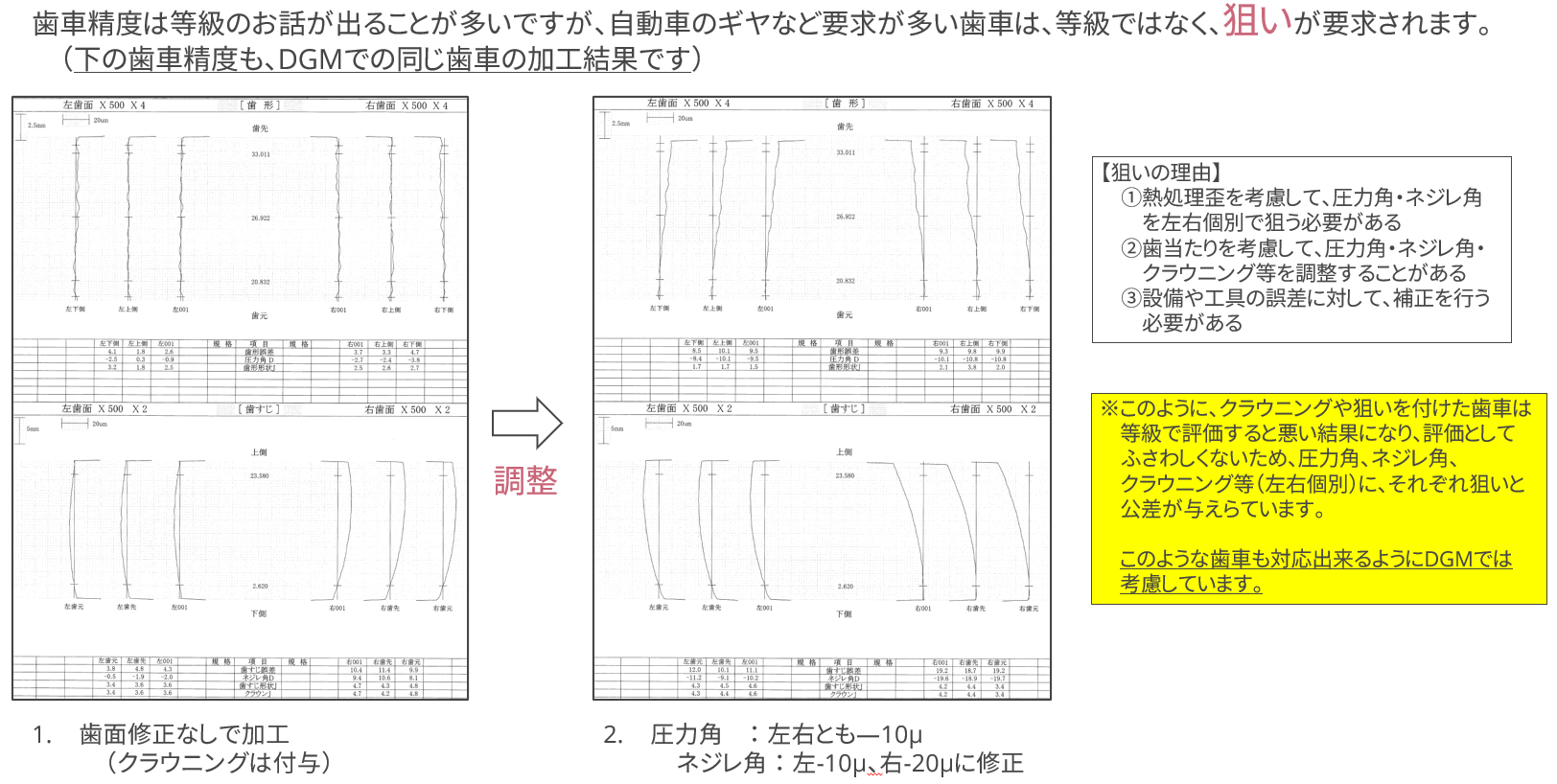
NCプログラム出力(設定)
NCプログラムの出力は、様々な設備に対応出来るように、テキストファイルの出力設定や、マクロ変数の設定、サブプログラムの番号の設定などを以下の画面で設定し、対称の設備毎に ”設備(設定)リスト” に保存して切り替えながら使用することが出来ます。
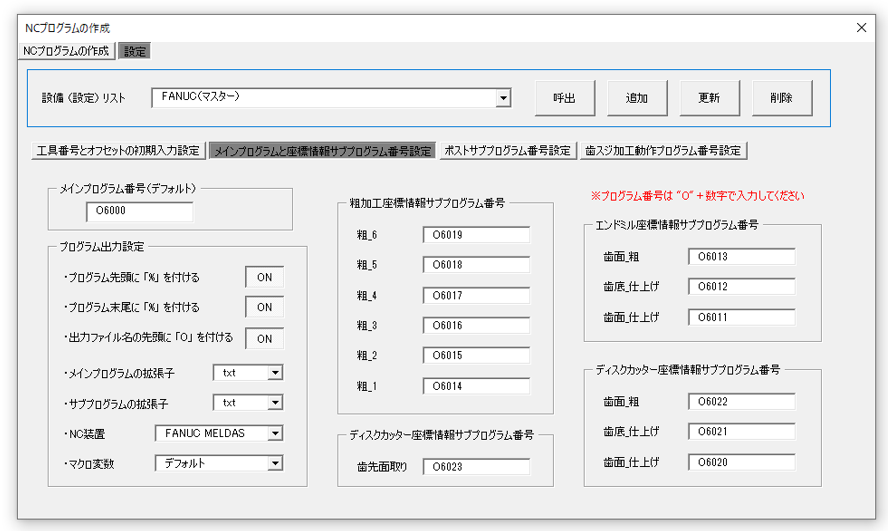
実際の加工実績からフィードバックした不具合対策
歯形不良対策
歯形不良の問題は最初に直面した問題です。
DGMは最初テーパーボールエンドミルで開発をスタートしました。エンドミルを使用した場合、歯底部の粗加工で歯底まで加工していくのが工具が細くなり難しく、下図のように歯底の粗加工を残したまま歯面の仕上げ加工を行うと顕著に歯形形状が悪化しました。理由は下図のようにテーパーエンドミルの根元の部分で歯面を加工して時にテーパーエンドミルの先端部が歯底と干渉し切削負荷で歯面に影響が発生します。
対策方法として歯面研削のプロチュバランスと同様に歯元部を粗加工で大きく加工し、歯面加工時の歯底干渉を無くすことです。この歯底形状の方が粗加工の工具の先端径が大きくなるので少し楽に粗加工を行うことが出来ます。
ディスクカッターの場合は、歯底の粗加工を行いやすく切削能力も高いので、歯形が崩れることは少ないですが、工具歯先の歯底干渉を避けるように工夫することを推奨しています。
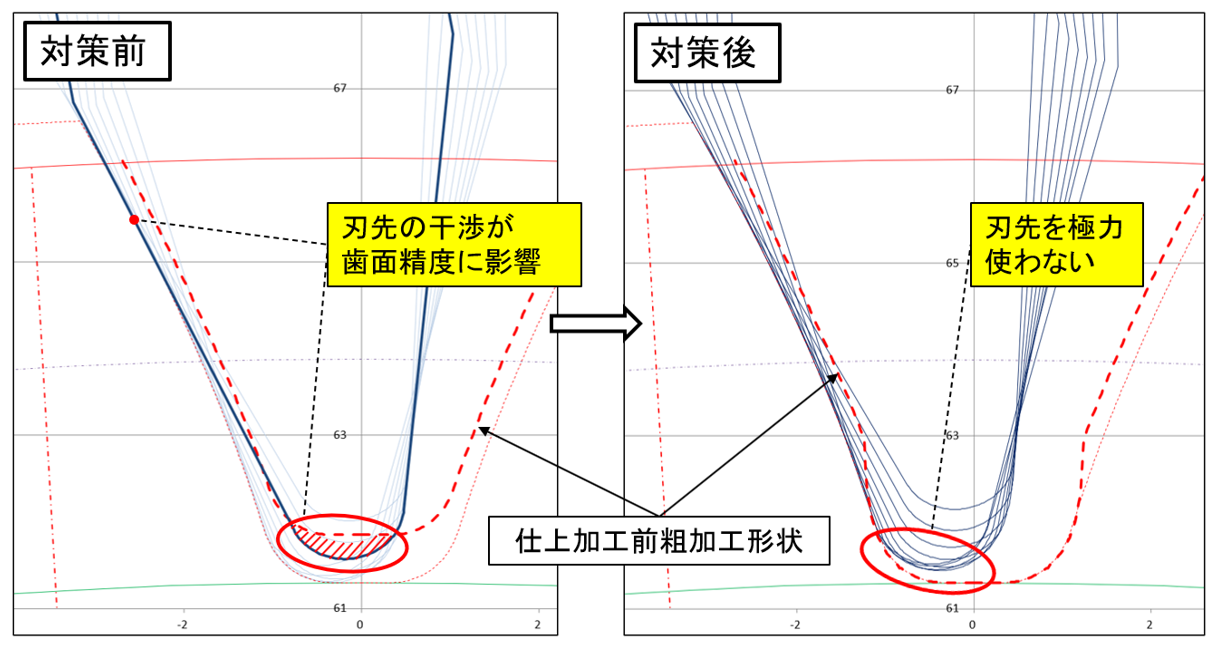
工具長不足対策(干渉対策)
特殊な諸元の歯車は標準の歯車より歯丈が高いことが多く、ホブカッターの通る軌跡に忠実にDGMカッターの加工パスを作成すると下図のように工具の刃長が不足して歯先まで仕上げることが出来ないという問題に直面しました。
そこで、下図のように歯先を加工するパスを工具の圧力角方向にシフトさせ加工する機能を追加しました。
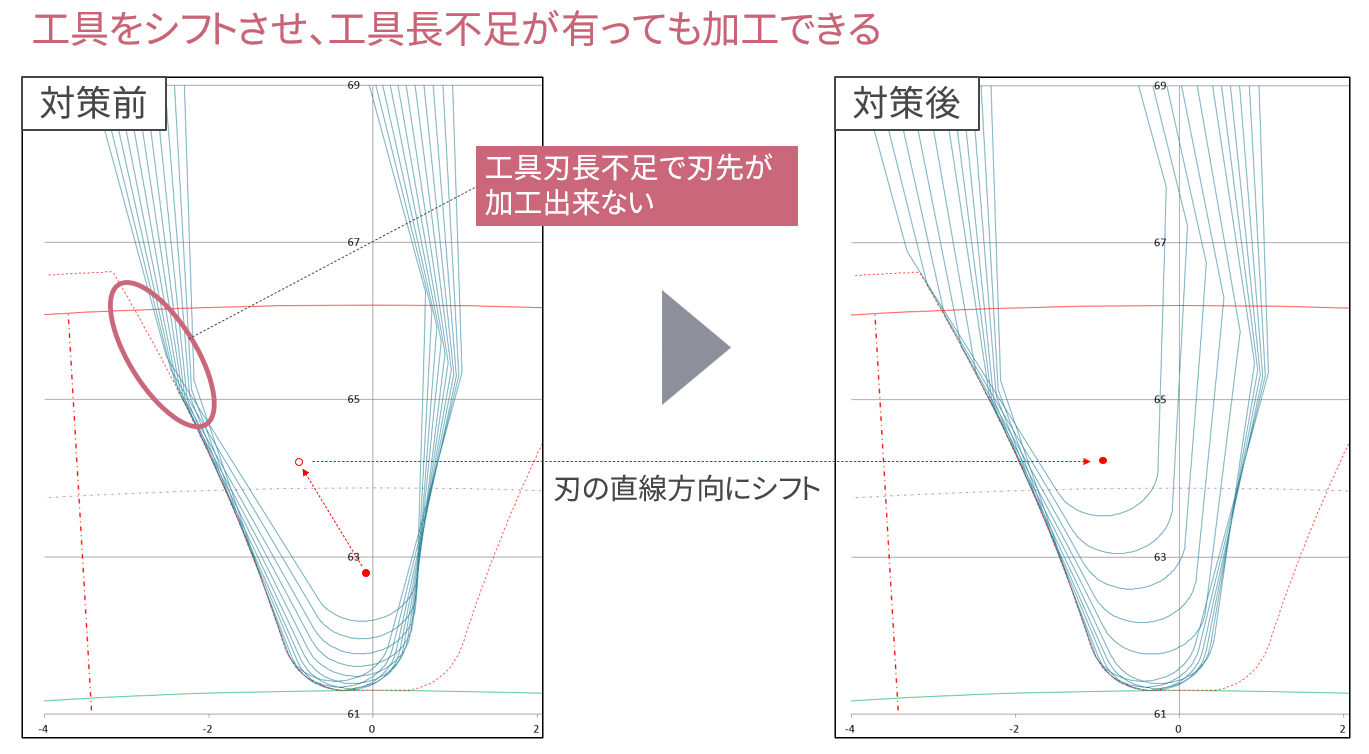
このシフト機能は下図のように、干渉対策にも活用することが出来ます。
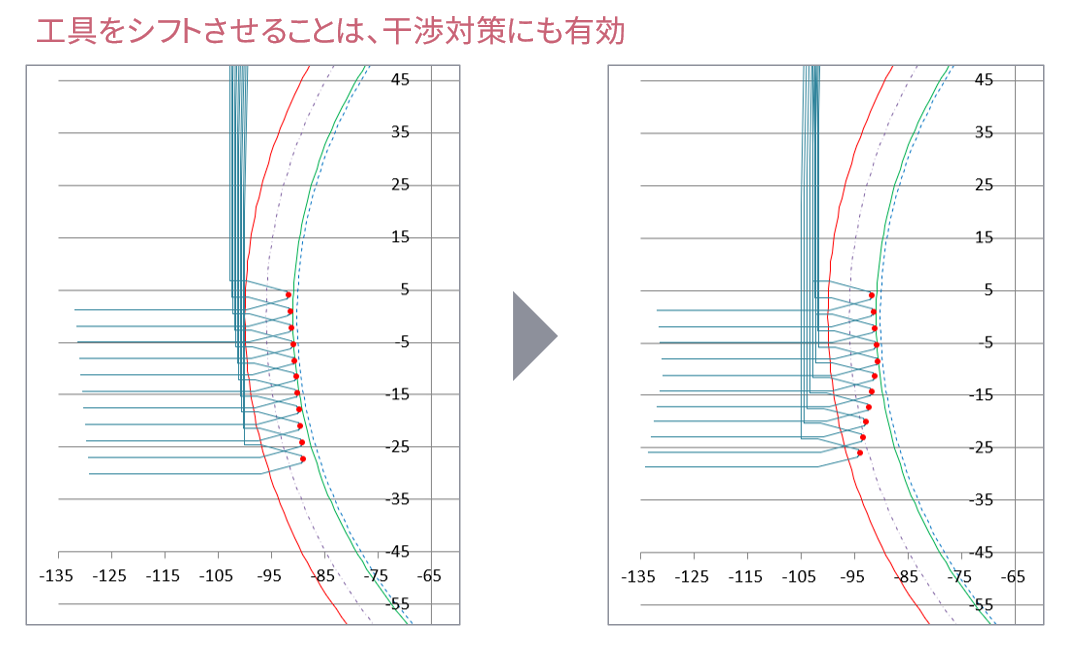
隣接ピッチ誤差不良対策
ディスクカッターの場合は、ほぼ問題になることは有りませんが、エンドミルの場合は歯車を1周加工する時に必ず摩耗が発生し、下図の”対策前”のような加工順序で加工を進めると加工開始歯と加工終了歯の間で隣接ピッチ誤差が悪化します。
"対策後"の加工順序なら、累積ピッチ誤差の値は変わらないですが、隣接ピッチ誤差の悪化は解消することが出来ます。
このような加工順序を簡単に選択できるようNCのサブプログラムで機能を追加しました。
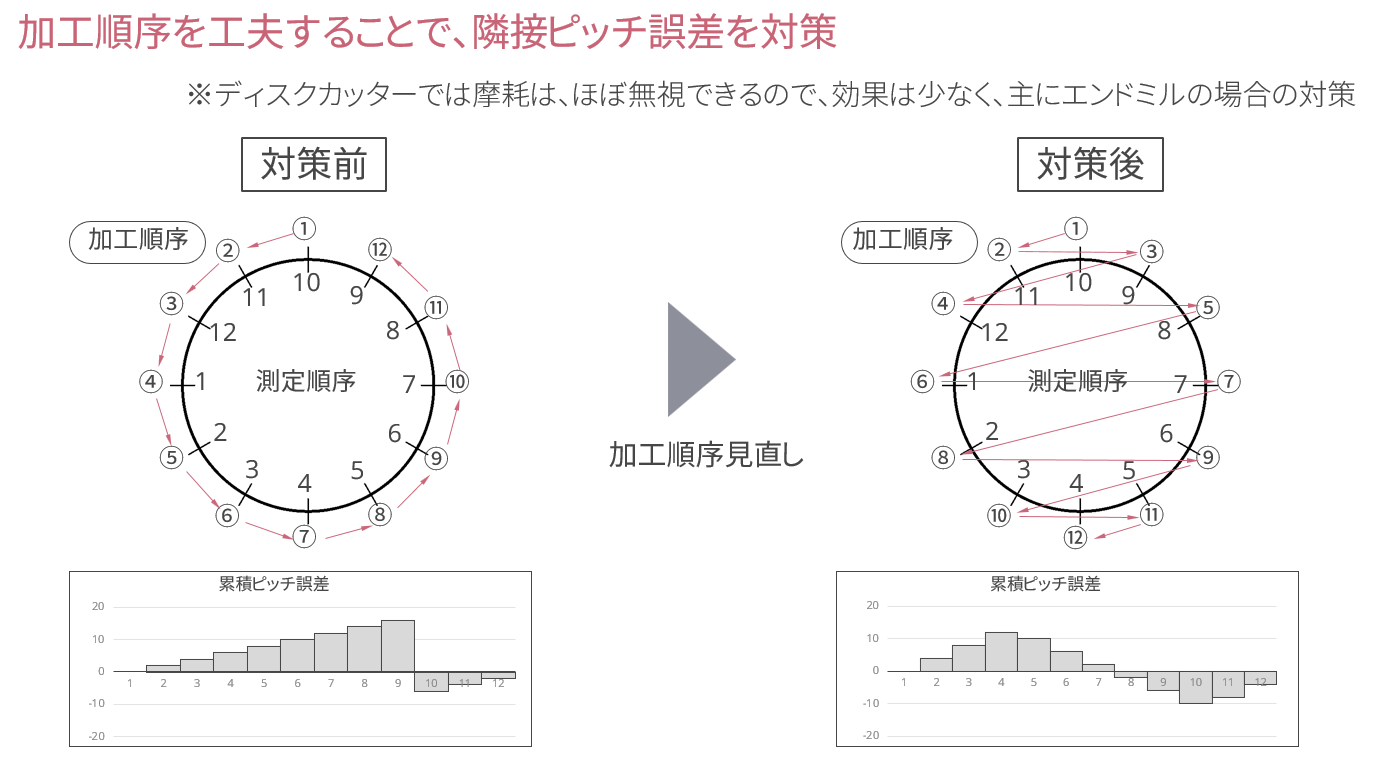
歯底FIT機能
DGMは量産時のホブ歯切の歯底形状を再現することを意識していますが、ホブの歯先RとDGM工具の刃先Rが一致していないと歯底形状を忠実に再現することが出来なくなります。そこで、”歯底FIT”の機能を追加して、創成のパスから少し外した位置に加座標を指示することで、歯底形状を忠実に再現できるようにしました。
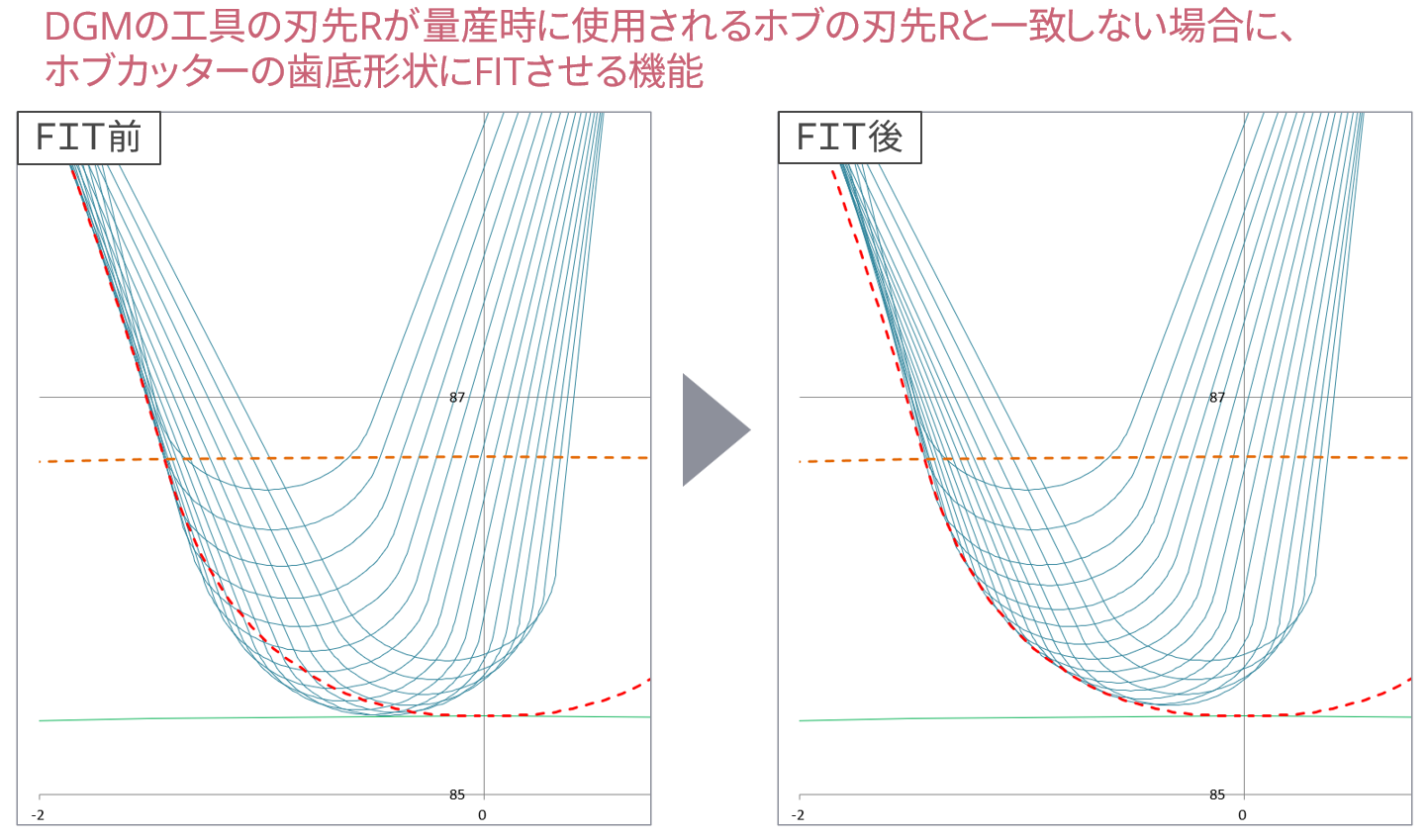
この”歯底FIT”を行うと歯面からパスが離れたり、歯底を加工する量が減ったりと、他の加工パスでその部分を補完することが出来ますが、少し影響は出るので、最近では他の2つの"歯底FIT"方法も追加して影響を少なくするように工夫をしています。
また、マーグやナイルスの歯面研削盤の考え方を利用して、”転位歯切”という機能も追加して歯底形状加工の柔軟性を向上させています。
追加の、2つの”歯底FIT” や "転位歯切" の機能については、日刊工業新聞社の「機械技術 2022年9月 特別増大号」に記事を掲載させて頂いたので、少し時間が経ってから本ホームページ上に記載しようと思っています。